高壓主汽調節閥接管焊接修復技術
某電廠百萬機組高壓主汽調節閥在進行材質檢驗時發現,進、出汽接管材質與設計要求材質不符,對機組的使用功能和安全保障有很大影響,需要更換和修復。本次修復將原有非對稱型坡口優化為對稱型坡口形式,采用分散焊接順序,在不妨礙裝焊的原則下適當加裝固定拉筋,防止修復過程產生焊接變形和位移;焊接過程中,嚴格控制預熱溫度和層間溫度,焊后及時進行熱處理。結果表明,焊接修復后的接頭組織為回火馬氏體,閥門變形在設計允許范圍內,焊接質量達到了JB/T4730-2005I級合格標準。
前言
某電廠1000MW機組高壓主汽調節閥在進行材質復驗時發現,進、出汽接管材質與設計要求材質不符,既影響電廠的安裝周期,又使主汽調節閥在運行過程中存在安全隱患。為了將影響程度降至最低,必須在最短的時間內完成接管的更換。由于1000MW高壓主汽調節閥結構和材質均比較特殊,是已發往電廠的成品,要在短時間內實現接管更換修復將面臨多方面的技術難題。
1、結構簡介
1000MW高壓主汽調節閥由四個主汽閥和四個調節閥組成,每個閥門連接一個接管,閥門本體材料為ZG1Cr10Mo1NiWVNbN,進、出汽接管材料均為P92鍛件。組焊工藝流程復雜、周期長,整套閥門組焊完耗時至少需三個月,整套閥門組裝后質量約80t。高壓主汽調節閥實物結構如圖1所示。

圖1 高壓主汽調節閥實物結構
2、技術難題分析
2.1、焊接性分析
閥門本體材料為ZG1Cr10Mo1NiWVNbN,屬于超低碳復相馬氏體鋼,焊接時淬硬性大,冷裂傾向明顯,容易形成脆化組織,成分為馬氏體和馬氏體+鐵素體組成的邊界區。冷卻速度較快時,易產生粗大馬氏體,焊縫熱影響區硬脆化;冷卻速度較慢時,易產生粗大鐵素體,焊縫熱影響區塑韌性顯著下降。P92鋼屬于低碳(w(C)=0.07%~0.13%)高合金(合金含量大于10%)耐熱鋼,淬透性很強,含碳量較低,其冷裂紋敏感性并不大,但對溫度較為敏感,須嚴格控制預熱溫度和層間溫度。
2.2、更換接管技術難度分析
如圖1所示,組焊后的主汽閥接管焊縫無法像單件閥殼焊接時實現橫焊位,只能采用全位置焊接。由于同時去除了四組主汽閥接管、四組調節閥接管,改變了原有工藝的焊接模式,若同時更換接管,因主汽閥1#和2#、3#和4#接管開檔距離為831mm,2#和3#之間距離為1232mm,如果四個管口同時焊接,操作時會產生干涉,另外,由于閥門空間狹小且加速器體積較大,射線探傷也會發生干涉。
閥門已精加工到位,閥體和接管焊縫必須“熱焊”,因坡口較深,焊接量大,很容易產生焊接變形。如果閥門變形,將直接導致閥門與閥蓋以及閥芯件無法裝配、密封,焊接變形控制非常難;電廠返回的閥殼是精加工件,焊后的熱處理只能采用局部回火,由于閥殼表面積較大,散熱面大且采用中頻熱處理時溫差較大,熱處理過程控制較難。
3、技術難題解決
3.1、接管焊接修復工藝
采用氧乙炔火焰加熱的方法進行焊前預熱,預熱溫度為250℃~300℃,使用測溫儀測量預熱溫度。采用石棉布包裹焊縫兩側附近的接管和閥殼本體,避免熱量散失。采用手工氬弧焊打底,焊條電弧焊填充、蓋面,焊接參數見表1,氬氣流量8~15L/min,直流正接,焊接速度20~35mm/min,每道擺動寬度小于等于10mm,每層堆焊厚度小于等于4mm,每焊完一層要及時進行清理。預熱溫度達到后開始焊接,層間溫度控制在300℃~350℃,焊接過程中不允許有任何缺陷。
表1 焊接參數表
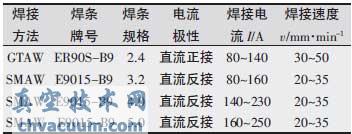
3.2、接管焊接坡口優化
如圖2a所示,原設計接管與閥殼焊接坡口為單邊30°V型非對稱形式,坡口深,焊接工作量大,焊接變形不易控制,焊接過程容易發生干涉。本次修復采用了如圖2b所示的坡口角度為16°的對稱型焊接坡口形式,焊接工作量小,焊接變形較易控制,節約了修復時間。
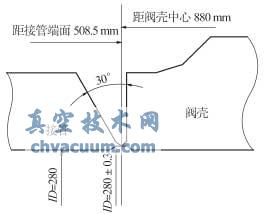
a優化前
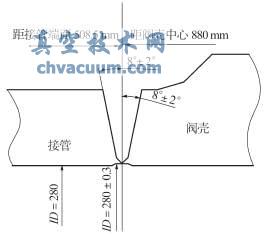
b優化后
圖2 主汽閥裝焊坡口優化
3.3、焊接變形控制
接管與閥殼為對接環焊縫,坡口深度約180mm,焊接過程中容易產生角變形,這將影響高壓主汽調節閥進、出汽接管與電廠管道的安裝精度,所以在修復過程中應嚴格控制接管與閥殼的焊接變形。主要采取了以下措施進行控制:
(1)裝配要求。坡口根部徑向及軸向錯位不超過±1mm,兩側坡口間隙為2mm,在不妨礙裝焊的原則下適當加裝固定拉筋,以防止焊接過程中產生變形和位移。
(2)焊接參數的選取。為減小熱量輸入合理控制焊接變形,焊接時盡量采用小線能量的焊接參數。
(3)焊接順序的確定及焊接變形的監測。為避免操作工對稱焊接時受操作空間的限制,在保證返修周期的前提下,采用分散焊接順序,優先裝配并焊接1#、3#主汽閥接管,再裝配焊接2#、4#接管。采用兩人對稱施焊順序,實行多層多道焊接,施焊中注意焊道間的交錯和結合,避免出現“死角”,并保持焊道平整,焊道布置示意如圖3所示。焊接過程中厚度方向每焊30mm須檢測接管與閥殼中心以及接管與接管中心相對尺寸。
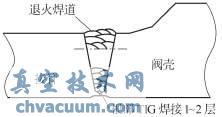
圖3 焊道布置示意
(4)降低溫度梯度。焊接時閥殼外部始終采用中頻感應加熱,內部采用柔性陶瓷電阻加熱片進行補熱,使工件焊接部位的溫度維持在200℃~250℃。
(5)探傷時間的確定。為降低返修焊接缺陷的風險,避免因重復返修焊縫而造成的焊接變形,在焊接至80mm深時停止焊接并進行無損檢驗,合格后方可繼續焊接。
3.4、焊后熱處理控制
由材料焊接性可知,ZG1Cr10Mo1NiWVNbN淬硬性大、冷裂傾向明顯,P92鋼對溫度敏感,為防止接頭產生缺陷,焊接后應及時對接頭進行熱處理。為了驗證修復后接頭的微觀組織,在焊接產品的同時,采用相同的工藝焊接試驗塊,并與產品同時進行熱處理。本次修復焊縫外部采用中頻感應加熱器,內部采用柔性陶瓷電阻加熱片補熱,溫度采用沿焊縫周向對稱布置的四只熱電偶進行監控。升溫速度不超過80℃/h,降溫速度不超過60℃/h(200℃以下不控制降溫,自然冷卻),為了充分得到回火組織,溫度控制在710℃~730℃,保溫8h。
試驗塊熱處理后的焊縫接頭微觀組織如圖4所示。由圖4可知,焊縫、熱影響區和熔合區均為回火馬氏體組織,具有良好的沖擊韌性和高而穩定的持久塑性及熱強性能。

a焊縫區

b熱影響區
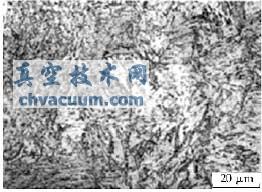
c熔合線
圖4 試驗塊焊縫微觀組織
4、接管更換后的產品檢驗
通過對焊縫布氏硬度(見圖5)進行檢驗可知,接頭硬度處于180~230HB,最大值位于焊縫中心區域。由此可知,經過熱處理后的焊縫獲得了與母材相近的硬度值。
經無損探傷檢驗,接管焊縫質量達到射線探傷標準和超聲波探傷標準Ⅰ級檢驗要求。閥殼形位公差檢驗結果如表2所示。由表2可知,各主要形位面的變形量均在設計要求的0.10mm范圍之內,滿足裝配要求。
表2 閥門各主要形位面變形量 mm

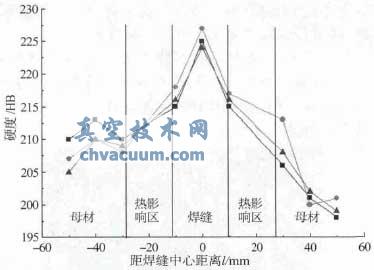
圖5 焊接接頭顯微硬度分布
5、結論
(1)百萬機組高壓主汽調節閥接管更換技術難度大,通過對ZG1Cr10Mo1NiWVNbN和P92材質對接環焊縫檢驗可知,本次修復有效地避免了裂紋等焊接缺陷的產生,焊后獲得了回火馬氏體組織,保證了焊接接頭的性能。
(2)將原有焊接坡口進行優化設計,采用分散焊接順序,并適當加裝固定拉筋,有效防止了修復過程產生焊接變形和位移,焊接順序合理。